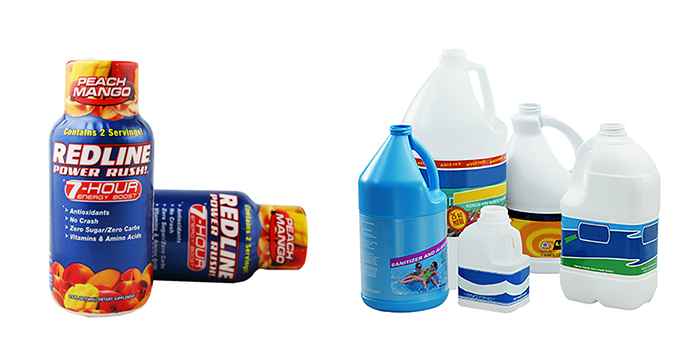
In our previous post on the topic of labels, we covered the importance of labels, essential questions to ask when considering the type of label for the product, and what machinery is needed to label primary and secondary packaging. We also took a deeper dive specifically into a popular type of label, pressure sensitive. Now, we’ll cover two other types of labels—shrink and stretch sleeves. While shrink and stretch sleeves are both commonly used for decorative labeling and do share some label similarities, they are different types of labels which will be explained in this review.
Unlike a pressure sensitive label, which is affixed on the product by an adhesive, shrink and stretch sleeves use no adhesive. Rather, with 360⁰ coverage, they are placed around a container from overhead or from the side and are held in place by some form of sleeve contraction.
Starting with shrink sleeves, they can be a desirable decorative label option because they have 360⁰ coverage and can also reach from the top to the bottom of containers, allowing maximization of available real estate on products. Shrink sleeves used on plastic bottles containing sports drinks, for instance, can cover the neck and shoulder and all the way down to the perimeter of the bottle’s base. Shrink sleeve labels add shelf appeal to the product, as the label can display a wide variety of colors and graphics, designs, and finishes from matte to gloss. Additionally, the product’s temperature or environment in which it is stored, such as a beverage stored in a refrigeration unit, is less of a concern compared to other label alternatives.
Shrink sleeve labels are typically made of polyethylene terephthalate glycol (PETG) film, because the film has a high shrink rate and conforms well to a multitude of different container contours. This film also works well with the most common container materials, such as metal, glass, and plastic. A vast range of products use shrink sleeve labels, including:
- Ready-to-drink beverages, such as sports drinks, energy shots, carbonated beverages, etc.
- Craft beers, wine, and spirits
- Condiments
- Processed foods
- Nutraceuticals
- OTC pain relievers, cough & cold remedies
- Cosmetics and personal care products
- Household cleaners, such as laundry treatments and fabric softeners
- Lawn & garden products
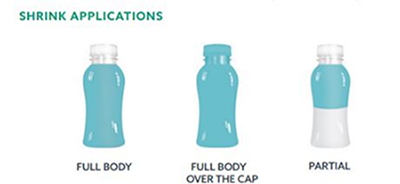
Shrink sleeves used as decorative labels have three general variations: full-body sleeves, full-body over-the-cap sleeves, and partial sleeves. A standard shrink sleeve (or full-body sleeve) covers much of the package but not the neck or cap. These labels are typically seen on plastic or glass bottles, metal cans, and more. As mentioned earlier, there are many reasons to use these, and it is also worth noting they can be a good alternative to printing directly on containers, as is the case with craft beer where blank cans can be purchased at bulk price and can then be used for any number of beers. A full-body over-the-cap sleeve covers the neck and cap of the package, as well as the perimeter of the bottom. Typically, this sleeve is used for plastic bottles like energy shots, ready to drink beverages that require a seal, personal care products, OTC cold remedies, and any other product that requires tamper evident coverage for security or consumer safety at the top of the container, in addition to a full body graphic sleeve. Partial sleeves, as the name suggests, covers only a portion of the container and are a cost-effective label alternative that mimic standard cut and stack, roll-fed, or even clear pressure sensitive labels. Partial sleeves are attractive for those who are environmentally conscious as it uses less plastic than traditional full body sleeves and can also highlight the color or contents of the product inside the container.
The process of shrink sleeving can be a relatively quick process. The PETG sleeve film is printed and measured to the exact size of the bottle with consideration for the extra room needed for shrinking and label distortion that occurs when shrinking. A conveyor delivers the bottles or containers down a line and places the package underneath the sleever. A sleeve is then positively applied on to the container vertically from above or horizontally from the side, with some machines running as fast as 800 containers per minute. From the sleever, the container gets conveyed to a heat tunnel where, in a matter of moments, the sleeve gets shrunk tightly to the contours of the container. This process is the same for all shrink sleeve types.
There are multiple types of heat sources that can be used in a heat tunnel: convection (forced air), infrared, and steam are the most common. Factors that should be considered when deciding on which heat to use for the label application include film type used, container material, product inside the container, environmental concerns, and product temperature at the time of sleeve application. Convective tunnels, the most popular due to their ease of use, utilize forced hot air and usually include a fan of some type to force air through a heat source, resulting in a heated air stream. Infrared tunnels utilize radiant heat to provide the energy required to complete the shrink process and utilize various energy sources from quartz panels or tubes. Infrared tunnels are normally used in conjunction with other types of tunnels as a finishing unit. Infrared is like steam in that it provides a consistent temperature and a high heat energy transfer. Steam tunnels use live steam to provide the energy required to complete the shrink process. The heat transfer is higher for steam and the shrink process occurs at a low, consistent temperature. Steam is recommended for most applications in which a sleeve is applied to a liquid-filled container, especially glass. *
Turning attention to stretch sleeves, while similar to shrink sleeves in being able to apply 360⁰ full color graphic labels without the use of adhesives, the material, application technology, and markets where they are used are different.
With stretch sleeves, no heat is required as part of the overall application process. Rather, each sleeve gets expanded and then slipped over the top of the product, being released at the point of desired height placement in one smooth motion. Therefore, the material used must have some elasticity to expand and then contract onto the contours of the container. A monolayer polyethylene (LDPE) material is commonly utilized. This material is resistant to moisture and chemicals, so if spillage occurs outside the bottle, the product won’t get trapped in the sleeve-like it could on a shrink sleeve. It also holds up better to product exposure which can be particularly important in cases where the product contains harsher chemicals.
Overall, stretch sleeving is a simple, flexible, and economical method of container decoration that is capable of covering round, square and rectangular containers. Like shrink sleeves, stretch sleeves can also cover a lot of container real estate, though, not as much as the full-body over-the-cap shrink sleeves. However, stretch sleeves are a good option for covering large containers like 2.5-gallon bleach bottles. Stretch sleeves are a popular label option for:
- General large bulk items
- Chemicals and cleaners
- Laundry detergents and bleach products
- Pet care, such as kitty litter
- Automotive fluids
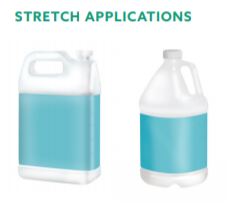
Typically, stretch sleeves are not as snug as shrink sleeves, and because adhesives are not used, products that use this label type are less concerned with minor label movement around the container. Additionally, while heat tunnels are not needed, stretch sleeving is normally slower compared to shrink sleeving with production rates at less than 150 bottles per minute on the high-speed side.**
Providing support to businesses needing or considering a shrink or stretch sleeve labeler is what Axon, a ProMach product brand, excels at. Axon manufactures machine applicators for just about every shrink and stretch sleeve label requirement and can determine which labeling machine will best suit the situation and desired outcome. With speed capabilities from high to low, from complete shrink sleeve lines to stand alone tamper band sleevers and heat tunnels, Axon’s robust lineup of solutions have made them a stand-out in this niche segment of the labeling industry. The link below provides more about Axon, the industries they serve, and more information on the technology behind shrink and stretch sleeving. Depending on your product’s size, label type, and speed requirements, there’s likely a shrink or stretch sleeve solution that can do the job.
* https://files.axoncorp.com/axon-tunnel-vision-selecting-the-right-heat-shrink-device.pdf
**https://redimark.com/packaging-primer-101-stretch-shrink-sleeve-labels/?=454038380603&=&=b&gclid=CjwKCAjwwab7BRBAEiwAapqpTLZmVdkU_8NW1W-zhdnKHPwvQcSMmrs-RD0xWLyY_EOT1aCxt4VEOhoC17cQAvD_BwE