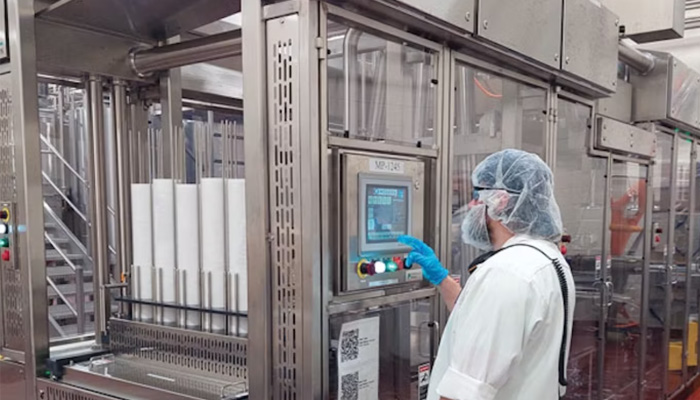
As consumer demand for high-quality, premium yogurt continues to rise, so does the pressure on processors to deliver consistent results at scale. One fast-growing dairy producer found itself at a crossroads: either upgrade its equipment, or risk capping its growth potential. With multiple formats, growing customer demand, and quality at the forefront, the company turned to Modern, a ProMach product brand, for a better solution. In a recent article on ProFood World, Michael Costa highlights the story and how Modern helped the production scale.
Outgrowing Legacy Equipment
Established in 2016 by Gunnar Birgisson, a former CFO of Coca-Cola Iceland, Reykjavik Creamery set out to introduce authentic Icelandic skyr to the U.S. market. Operating on a 400-acre organic dairy farm, the company began its production journey in 2019 with a modest rotary filler, capable of processing 60 cups per minute. While this setup was suitable for initial operations, it soon became evident that the equipment couldn’t keep pace with the growing demand and required frequent maintenance, leading to significant downtime. Even an intermediate upgrade to a three-lane filler proved difficult to operate and lacked the performance needed to meet increasing demand.
Like many processors scaling up, they needed something more: a hygienic, efficient, and user-friendly solution that could handle both single-serve and multi-serve yogurt cups with accuracy and minimal changeover time.
Precision Filling Meets Scalable Design with Modern
Reykjavik then invested in a six-lane inline filler from Modern, built for speed, flexibility, and food safety. Equipped with real-time weight feedback using individual load cells, this filling system minimizes product giveaway while ensuring accurate fills across formats.
A clean-in-place system (CIP), efficient lid placement, and easy-to-adjust pistons made the machine ideal for handling yogurt’s thick consistency without slowing down operations. A touchscreen HMI streamlined operation, reducing training time and enabling consistent performance across shifts, even without experienced operators on every line.
However, what truly stood out was the inclusion of a HEPA air filtration system, designed to reduce airborne contaminants around the fill zone, thereby helping to maintain shelf stability and product quality, even in high-volume dairy environments.
Triple the Output Without Expanding the Team
With the new Modern filling system fully integrated into the line, daily production jumped from 50,000 to 140,000 cups per shift—nearly tripling output within the same 10-hour window. The company didn’t need to add labor or extra shifts to make it happen. The equipment’s reliability and efficiency even allowed them to take on larger customers with high-volume requirements.
And thanks to Modern’s robust build and responsive technical support, the transition was smooth. Operators adapted quickly, and any issues during ramp-up were quickly addressed by Modern’s service team, reinforcing the equipment’s long-term value.
Why Modern? Built for Dairy, Designed for Growth
Modern’s inline and rotary filling systems are trusted across the dairy and food industries for a reason. With support for ultra-clean, MAP, and aseptic configurations, these systems are built to exceed sanitary design standards and operate reliably under pressure. Whether you’re producing yogurt, dips, sauces, or other viscous products, Modern offers equipment designed for flexibility, speed, and long-term growth.
If you’re looking to expand your dairy packaging line—or streamline your contract manufacturing operations—Modern’s filling technology could be the catalyst for your next leap forward.