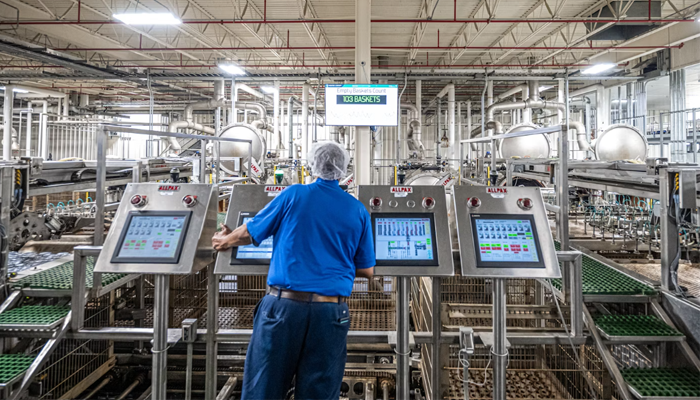
A new article in ProFood World written by Joseph Derr highlights the results of retort automation at Crider Foods, a leader in canned protein production. Crider sought advanced retort automation for business growth and to stay ahead in a rapidly growing competitive market. By implementing an advanced retort system from Allpax, a ProMach product brand, Crider has significantly transformed its production processes, upskilled its workforce, and increased its environmental sustainability efforts with reduced water consumption.
Crider Foods relied on a manual retort process for many years, which presented several challenges as demand for their products increased. The company needed to scale up its operations to maintain high production levels, which meant finding a more efficient way to handle the retort stage. This stage, responsible for sterilizing canned goods, was time-consuming and relied on manual processes.
A New Era of Automation
Crider turned to ProMach product brand Allpax, a leading supplier of retort processing solutions that specialize in automated retort systems designed to handle the high demands of food processing with efficiency.
“The Crider retort room now features 15 Allpax static retorts for cans and five dual-mode retorts capable of saturated steam and water spray with overpressure, which are used for cans or for the new pouch lines of ready-to-eat chicken products. From the time the empty cans are depalletized to the time the full cans are packed into trays and palletized, no human touches them,” writes Derr.
The system automates the loading, unloading, and handling of retort baskets, which significantly cuts down on the manual labor required. The automated retort loaders ensure that each cycle is optimized, reducing any chance of missteps or errors that could happen in manual handling.
Efficiency Meets Quality and Safety
Consistency is key in food processing, especially for companies like Crider Foods, where the uniform sterilization of products is crucial. The automated system provides this consistency by ensuring that each batch is treated with the same precision and care, eliminating the risks of variability and human error.
Automation has improved workplace safety by reducing the need for employees to manually load and unload heavy retort baskets, which can be physically demanding and pose risks for injuries over time. With robotic systems handling these tasks, employees can focus on overseeing operations, improving both productivity and worker safety.
Additionally, the automated retorts use less water and energy per cycle compared to their manual predecessors, contributing to more sustainable production practices. “Retorts are the largest consumers of water at Stillmore, mostly from cooling the cans after processing,” writes Derr. “The plant added filtration/recycling systems and has reduced water consumption by 66%. Outside the retort room, washing cans offers another opportunity to cut consumption and operation is examining other ways to cut down on use.”
For Crider Foods, automating their retort system is just one example of how adopting innovative technology can help a company thrive. This upgrade solves their current operational challenges and sets the stage for future growth. As consumer demand continues to rise, Crider is well-positioned to scale its operations and maintain its competitive edge in the canned protein market.
Click here to read the full article and in depth details on ProFood World.
And click here to learn about Allpax Automated Batch Retorts.