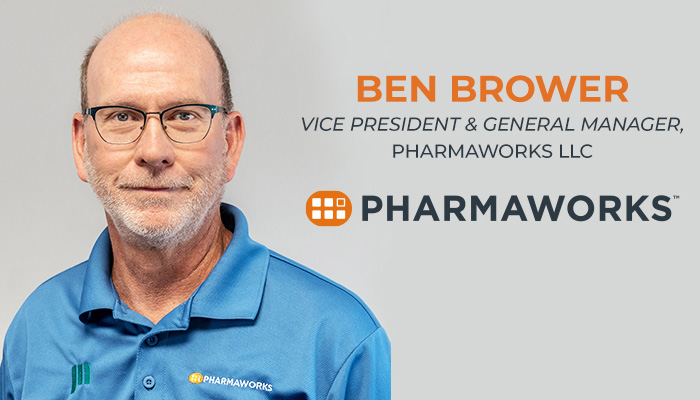
In a recent interview in Nutraceuticals World, Ben Brower, Vice President and General Manager of Pharmaworks, discusses the increasing demand for blister packaging machinery for gummy supplements and its role in new packaging concepts for gummies. In fact, Brower has heard reports from customers and OEMs alike that their manufacturing capacities are nearly sold out for the rolling 12-month period starting Q4 of 2022 for gummy packaging.
Pharmaworks is a ProMach product brand and leader in manufacturing innovative blister packaging systems for the pharmaceutical, nutraceutical, animal health, medical device, consumer goods, and contract packaging industries.
When asked about the advantages of blister packaging for gummies, Brower highlighted several key points. Blister packaging offers a unit dose type package, with each blister cavity containing one piece of product. This allows consumers to take a single product without compromising the others on the blister card. Cavities can be individually labeled with important information such as lot and date coding, product name and strength, and barcoding, ensuring clarity for consumers. Additionally, blister packaging provides security, compliance, and patient convenience, as each individual cavity/unit of dose ensures product integrity and enables patients to track their consumption.
As gummies are widely used for nutraceutical products, Pharmaworks has discussed with gummy processing OEMs about using the gummy technology but putting medical APIs in the formulation. Designing gummies to resemble traditional oral solid dose products aims to prevent children from mistaking them for candy. Gummies are chewable and can be a suitable delivery method for older patients and children.
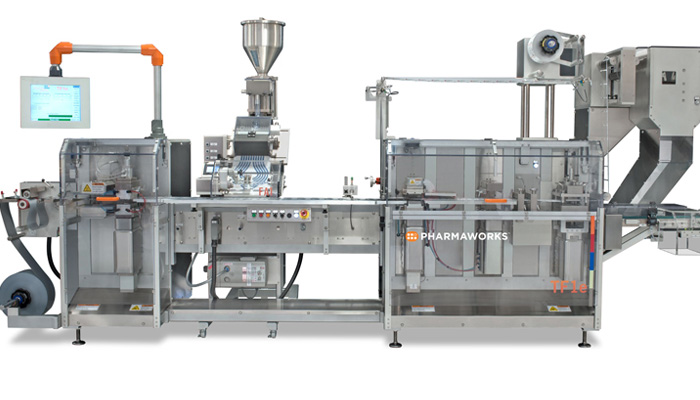
Brower also discussed potential improvements in the traditional process of forming, molding, and packaging gummies. “Traditionally, the gummy is a hot-pour or dispensed into standalone molds. The molds are then accumulated, allowing time for gummy products to solidify. Molds are emptied and gathered as bulk to be packaged,” Brower states.
“One concept to reduce the number of steps required is to dispense the product into molds that are indexed on an automated carousel. These indexed molds can be directly cooled while in motion. This automation can be in proximity if not directly coupled to a blister machine. Products can be picked from the indexed molds and fed directly into blisters. Pharmaworks has experience feeding these types of products directly into our family of blister machines. Blister rates can be scaled from 50 BPM on the TF1 blister machine to over 300 BPM on our TF3 blister machine.”
Read more of Brower’s expert insights on the increasing interest in blister packaging for gummies, the benefits it offers in terms of labeling, security, compliance, and shelf life, as well as potential improvements in the molding and packaging processes to enhance efficiency and convenience.
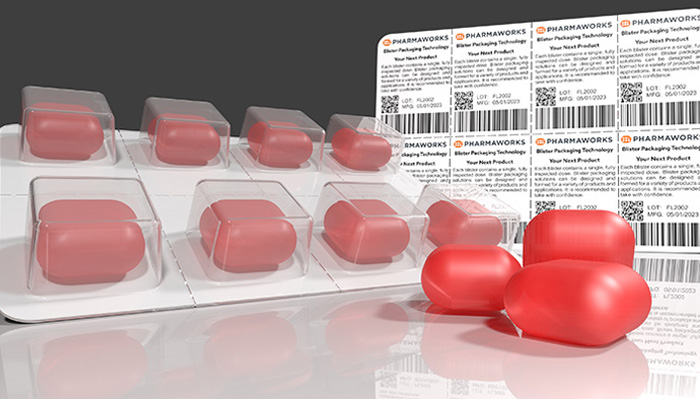