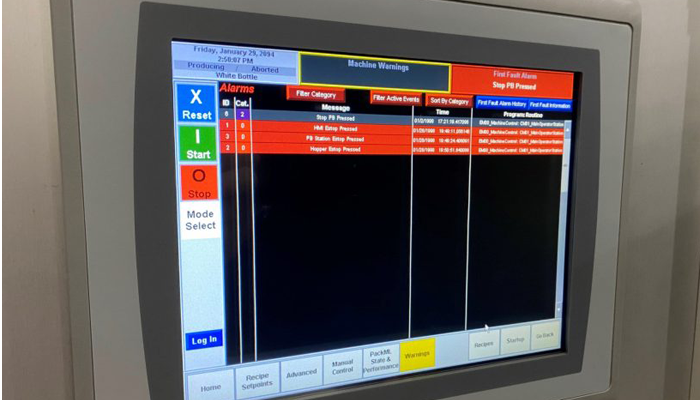
Written by Frank Volpe VP & General Manager, Zarpac
Zarpac, a ProMach product brand and a recognized industry leader for integrated, OEE availability optimized turnkey packaging lines, turnkey bottle lines, packaging line engineering services, and custom packaging equipment design-build capabilities, is known in the industry for designing, integrating, optimizing, installing, commissioning, and handing-off packaging lines that run at promised line availability and OEE targets. We do that by preventing the problems that other packaging line designers and integrators unintentionally build into their lines.
Our approach is focused on helping customers optimize line availability by avoiding the 5 Deadly Mistakes of Packaging Line Design and Integration.
The impacts of these 5 Deadly Mistakes are easy to understand but preventing them requires deep packaging equipment and packaging line design and implementation expertise.
Our understanding of these mistakes and their costly impacts has been derived in part by the hundreds of “clean up this mess” packaging line projects we have been retained to fix. Our team has completed several hundred such projects over the last thirty years and everyone has enhanced our understanding of what works, and what doesn’t.
Here Are the Top 5 Deadly Mistakes of Packaging Line Design and Integration:
- Incorrect machine placement in the line
- Incorrect steady state and surge machine speeds
- Incorrect accumulation design and capacity
- Ignoring conveyor system integration
- Ignoring product, primary packaging and secondary packaging characteristics
Just one of these detrimental mistakes can cause extremely costly downtime, lost production by below target production speeds, and reduced productivity.
When you begin evaluating potential suppliers for your next packaging line project, we encourage you to ask them about how they will guarantee you will not have to live with the downtime and lost productivity caused by these deadly mistakes.
1. Incorrect machine placement in the line.
The distances between each piece of equipment in a packaged goods production line are critical to the overall performance and OEE of the line. Incorrect machine placement refers to the mistake of placing pieces of equipment too close together, too far apart, or too close to conveyor direction changes.
Incorrect machine placement can prevent a production line from achieving steady-state running conditions. Lines that cannot reach steady-state production rates experience higher rates of unnecessary machine stops, resulting in lost production, lost operating efficiency, increased product jams as well as premature machine wear.
What happens when machines are not optimally placed in a packaging line? The most common negative OEE impacts are:
- Starved machines
- Blocked machines
- Chronic start-stop-start line operation
- Chronic ramp-up, ramp-down, ramp-up cycling
- Below target production speeds
- Down containers
- Container jams
How do we avoid making this mistake?
Zarpac protects customers from the pain of this mistake by using proven, validated packaging design tools. Our Packaging Line OEE Optimization Model is a proprietary tool whose outputs guarantee that a specific line design and layout does not negatively impact OEE.
One of the key outputs from this tool is precise inter-machine placement distances as well as optimum conveyor speeds and the precise placement of line control sensors. Our engineers started developing this tool over twenty-five years ago and since then it has been used, tested, challenged, upgraded, expanded, validated, and used again and again.
Our Packaging Line OEE Optimization Model and a dozen other proprietary Zarpac tools replace the guesswork, the opinions, and the conventional wisdom used by other suppliers with validated formula-based tools that convert production line requirement inputs into practical design criteria.
Packaging line design, integration, and optimization is a science, not an art, and our proprietary formula-based tools deliver accurate, consistent, and on-target results.
Experience has taught us and our repeat customers that numbers, when used correctly, never lie.
2. Incorrect steady-state and surge machine speeds
Calculating and setting optimum steady-state and surge machine speeds for every container on the line and every machine in the line is essential to steady-state line operation.
Incorrect Steady-state and Surge Machine Speeds refers to the mistakes of:
- Blindly using a V-curve model to establish machine speeds.
- Not accurately calculating and setting individual machine speeds to optimize operation of line accumulation capacity.
Too often vendors use a simple V-curve approach for setting machine speeds which seems perfectly logical. Unfortunately, this approach frequently results in machine speeds and surge speeds that do not take into account the complex interrelationships of every machine and every accumulation zone on the line.
For many vendors, the V-curve approach is the window dressing used to disguise opinion-based speed settings, or even worse, the speed settings they used on the last line they did that was similar to yours. Either way, these approaches open the door for a costly mistake to enter the line during the design process
What happens when steady-state and surge speeds are not calculated for optimum performance?
The most common negative OEE impacts are:
- Starved machines
- Blocked machines
- Discharge side accumulators are always full during steady state operation
- Infeed side accumulators are always empty during steady state operation
- Accumulators are slow to fill and slow to empty
- Chronic start-stop-start line operation
Each of these impacts creates downtime, slows down the line, and prevents steady-state operation. This translates into reduced productivity, lost revenue, higher labor costs, and a longer than planned return on your investment.
How do we avoid making this mistake?
Our Optimized Machine Speed Calculator and Packaging Line OEE Optimization Model are proprietary tools whose outputs guarantee that a specific line design and layout does not negatively impact OEE. Key outputs from these tools include precise, steady-state, and surge machine speeds for every machine and every container to run on the line.
Based on the outputs from these tools we guarantee that customers will not live with the downtime and lost productivity caused by the Costly Mistake of incorrect steady-state and surge machine speeds.
3. Incorrect Accumulation Design and Capacity
Designing and sizing accumulation systems and programming them to operate seamlessly with line conveyors and the machines in the line is as essential to line performance as the machines themselves.
Incorrect Accumulation Design & Capacity refers to the mistakes of:
- Under-sizing accumulation capacity
- Over-sizing accumulation capacity
- Omitting accumulation where is it needed
Too often vendors simply guess where and how much accumulation is required in a line. Or they rely on conventional wisdom which is often no more effective than a guess.
Symptoms: What happens when accumulation is incorrectly sized or missing altogether?
The most common negative impacts are:
- Undersized accumulation – Results in unnecessary line stops leading to no steady state production
- Missing accumulation – Results in unnecessary line stops leading to no steady state production
- Oversized accumulation – Wasted $ and wasted space
- Accumulators are slow to fill and slow to empty – Delays return to steady state production
- Wrong accumulation technology implemented – Incompatibility with primary and secondary packaging causes downtime and damaged containers
How do we avoid making these mistakes?
ZARPAC uses proven, validated packaging design tools to protect our customers from this mistake.
Our Packaging Line OEE Optimization Model and Optimized Accumulation Sizing Calculator replace the guesswork and opinions used by other suppliers with validated formula-based tools that convert production line requirement inputs into practical, quantified design criteria.
Accumulation design, placement, and sizing is a science, not an art, and our proprietary formula-based tools deliver accurate, consistent, and on-target results.
Experience has taught us three very simple accumulation equations:
- Undersized Accumulation = Downtime + No Steady State Production
- Oversized Accumulation = Wasted $ + Wasted Space
- Missing Accumulation = Downtime + No Steady State Production
4. Ignoring Conveyor Integration
Designing a conveyor and programming the entire conveyor system to work seamlessly with the machines in the line is as essential to line performance as the machines themselves. Ignoring conveyor integration refers to the mistake of treating conveyors as less important to line performance than the machines in the line.
Too often vendors providing packaging lines ignore the importance of conveyor integration and they supply dumb conveyors, incorrectly configured conveyors, or poorly programmed and controlled conveyors.
Experience has taught us a very simple equation: No Conveyor Integration = No Steady State Production.
Symptoms: What happens when conveyor systems are not properly designed, programmed, and fully integrated into the production line?
The most common negative OEE impacts are:
- Excessive back pressure – damages containers and creates jams
- Excessive back pressure – increases occurrence of down containers
- Excessive back pressure – causes premature wear of line components.
- Chronic start-stop-start line operation – reduces output
- Chronic ramp-up, ramp-down, ramp-up cycling – reduces output
- Below target production speeds – reduces output, lowers OEE
- Lines never achieve steady-state production
- Some products produced on the line do not run reliably or consistently
Why do these bad things happen?
- Conveyor speeds are not synchronized with machine speeds.
- Conveyors are blind to downstream or upstream line conditions due to sensor placements, poor programming or both.
- Conveyor surge speeds are not synchronized with accumulation.
- Conveyor layout is not optimized for required steady-state or surge speeds.
- Conveyor is not controlled by a fully programmed, dedicated PLC.
How do we avoid making this mistake?
Zarpac protects customers from the pain of this mistake by treating conveyor integration the same way we treat every machine in the packaging line.
The process of protecting customers from this deadly mistake begins with the line layout and the specifications for conveyor speeds, conveyor types, line control sensor placements, and conveyor control systems. The attention we pay to this process is essentially identical to the attention we pay to every machine in the line.
When defining these specifications, the desired steady-state speeds of every machine in the line, as well as their surge speeds and ramp-up and ramp-down times are all inputs to the design process.
Based on the defined specifications, we select the optimum controls platform including the PLC, the HMI, the VFDs, and all supporting controls electronics. Then we design and build the panel.
Experience has taught that turning over this critical deliverable to third parties just doesn’t work. Every conveyor system is different, and sensor placement along with the line controls must be designed and optimized for that system.
And last but not least, our controls engineers program, run, test and commission the controls system as part of the overall packaging line commissioning process. As with the control panels, we never use third parties for programming services.
5. Ignoring product, primary packaging, and secondary packaging characteristics
The products being packaged, and the primary and secondary packaging being used to pack them can have a huge impact on line design, integration, and ultimately line performance. Ignoring product & packaging characteristics refers to the mistake of not thoroughly evaluating empty and full packaging characteristics and designing the packaging line to accommodate these characteristics.
If the characteristics of every product and packaging type to run on the line are not evaluated and addressed in the line integration process, bad things can happen.
Symptom: What happens when product and packaging characteristics are ignored or not thoroughly evaluated?
The most common negative OEE impacts are:
- Some products and containers run great, others don’t – reduces productivity and line OEE
- Down containers – increased downtime
- Container jams – increased downtime
- Excessive secondary packaging equipment downtime
- Excessive secondary packaging material scrap
- Damaged containers
Why do these bad things happen?
- Failure to understand or evaluate the different characteristics of empty versus full containers.
- Failure to select machines capable of efficiently running all container sizes and shapes to run on the line.
- Failure to optimize conveyors for all container sizes and shapes to run on the line.
- For packaging lines running more than one product and one container, ignoring these variables will negatively impact line OEE and overall productivity.
- Failure to optimize conveyors for all container types and materials to run on the line:
- Some containers are stable and easy to handle. Some are not
- Some containers are rigid or semi-rigid, some are flimsy.
- Some containers have low coefficients of friction, some have high coefficients of friction.
- Some containers have multiple labels, some have one.
How do we avoid making this mistake?
Zarpac protects customers from the pain of this mistake by thoroughly evaluating every product, every primary package, and all secondary packaging as part of the line design and integration process.
The process of protecting customers from this deadly mistake begins with the line layout and the specifications for conveyor types, line control sensor placements, and conveyor control systems. The attention given to this process is essentially identical to the attention we pay to every machine in the production line.
We identify product handling risks through brainstorming sessions with multi-disciplinary teams. The end result is a detailed list of risks and an action plan of how to minimize or eliminate those risks. This process frequently involves the development and use of test stands to simulate line conditions and to validate product handling solutions.
To learn more about Zarpac and their turnkey packaging lines, engineering services and line design, and custom packaging equipment design and build, head to their website: http://www.zarpac.com