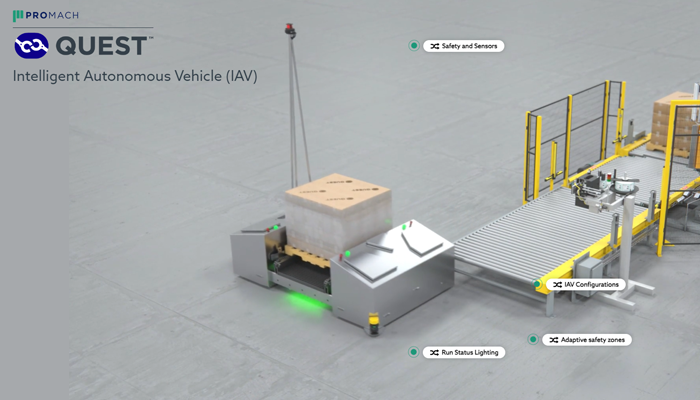
Autonomous Guided Vehicles, or AGVs, have emerged as a crucial technology in robotics and automation, capturing the industry’s attention for their transformative potential. AGVs represent a leap forward in how businesses approach logistics and material handling, blending sophisticated robotics with automation and human interaction to enhance efficiency, safety, and operational fluidity. As industries strive for greater productivity and leaner operations, AGVs offer innovative solutions to traditional challenges. Their rising popularity and adoption across various sectors underscore the growing recognition of their value in a future driven by automation and smart technology.
Unsurprisingly, the demand for autonomous vehicles in the market has surged. Their growth is projected to increase at a CAGR of 8.7% between 2023 and 2033, reaching a total of US$ 70,331.5 million in 2033, according to a report from Future Market Insights*
Quest, a leader in manufacturing industrial automation equipment focusing on robotics and vision guidance, launched its Intelligent Autonomous Vehicle (IAV), and theirs boasts significant advantages compared to other automated material flow solutions. The Quest IAV is designed for large payloads and follows predetermined paths to execute commands while maneuvering around obstacles if required. The IAV saves time and money because it eliminates physical guides and installation of the tape, rails, reflectors, etc. It improves efficiency because it can move entire pallets in one trip.
We recently had the opportunity to talk with Erik Grinnell, Vice President of Automation at Quest, who played a pivotal role in orchestrating the development of the Quest IAV. When joining Quest almost nine years ago, Grinnell and the Quest team took on the challenge of transforming the drawbacks he had experienced with robotic self-driving vehicles in previous organizations. He wanted to design and build a more advanced platform, leveraging their expertise in palletizing equipment and integrating the IAV line to provide a comprehensive solution as the OEM.
Grinnell provides a unique perspective on the development process of the IAV. From conception as a solution to various industry challenges, Quest’s proactive approach to addressing these issues with innovative solutions underscores Quest’s role as a leader in the field.
ProMach: What were the key challenges in the robotics industry that you aimed to address with the creation of the IAV? Did you try to solve a problem that you didn’t see a solution to in the marketplace?
Erik Grinnell: Our primary objective was to develop an intelligent vehicle built on an exceptionally stable chassis, capable of accurately transporting multiple pallets (up to 3) over long distances. To achieve this, we employed the highest quality components in the industry, resulting in a remarkably robust vehicle. The seamless integration with our existing product lines and other ProMach brands played a pivotal role in our success.
PM: How did you balance the need for maximum efficiency with rigorous safety standards in the design of the IAV?
EG: The vehicle prioritizes safety from its foundational design, with the chassis specifically tailored to accommodate safety features. Beyond industry-standard safety scanners, we incorporate extra lidar sensors, pallet overhang sensors, pause buttons, estops, and continuous redundant monitoring, ensuring the vehicle remains secure at all times.
PM: Safety is a critical aspect of autonomous vehicles. How does the IAV adhere to or exceed current safety standards?
EG: The IAVs adhere to and surpass existing guidelines for self-driving industrial vehicles, as specified by ANSI B56.5, B56.8, and NFPA 505 (Fire Safety). We employ top-notch components to ensure both the vehicle and operators’ safety.
PM: Can you provide an example of a safety challenge you faced and overcame during the development of the IAV?
EG: An insightful safety challenge we encountered during development was the limitation of safety scanners, which excel in a 2-dimensional plane with the vehicle. To address this, we incorporated extra lidar scanners at both the front and rear of the vehicle, expanding the detection capability to objects beyond the confines of that 2-dimensional plane.
PM: Could you talk about how the IAV integrates with other systems in a facility and how it enhances overall operational productivity?
EG: Within the IAV system, there is a central control panel referred to as the command station. This station seamlessly integrates with both new and existing equipment, such as Palletizers, Stretch wrappers, ASRS, etc. It takes on the responsibility of calculating the most efficient route, choosing a suitable vehicle, and orchestrating the execution of pickup and dropoff commands. The command station embodies a significant level of intelligence, functioning as the pivotal “traffic controller” in the system.
PM: In what ways do you think the IAV is pushing the boundaries in the field of robotics and automation? Versus the AGVs and AMRs?
EG: While the majority of AGVs and AMRs are designed to handle a single pallet load, our system stands out as it efficiently moves 1, 2, or 3 pallets simultaneously over considerable distances, often spanning thousands of feet. This approach significantly diminishes the overall fleet size required. Additionally, our innovations extend to enhancing vehicle stability and optimizing drive characteristics, especially for maneuvering large vehicles in confined spaces.
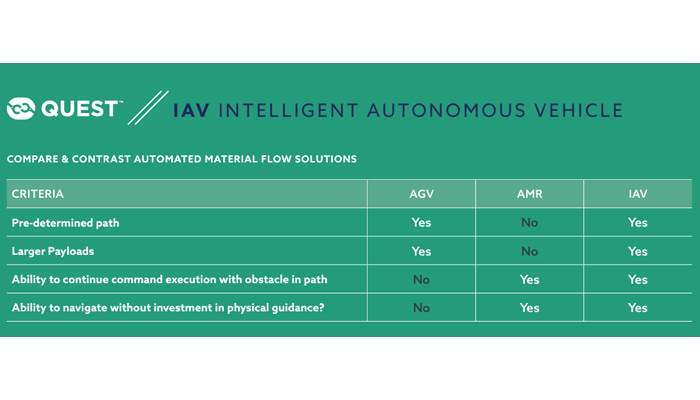
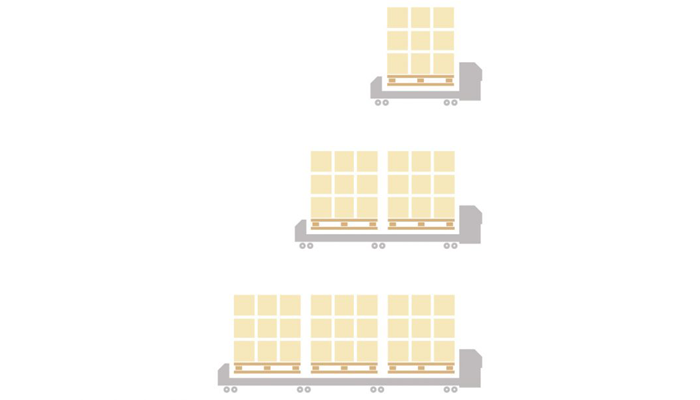
PM: What role does user feedback play in the ongoing development and improvement of the IAV?
EG: Maintaining a direct connection with customers for feedback is crucial, especially with our expanding product lines. Our commitment to delivering top-notch equipment drives us to continuously learn and evolve. We make regular visits to customers using our new product lines, identifying improvement opportunities. We not only develop these enhancements but also provide retrofit options, ensuring a path for continuous improvement.
PM: Are there any aspirations for the next generation of IAVs? Are there any specific advancements or features you’re excited about?
EG: Our latest generation of vehicles has just been launched and is currently making its way into the field. Building on our proven technology for navigation, drive kinematics, etc., we have enhanced it further with both mechanical upgrades and advanced diagnostics, incorporating user-friendly features for improved ease of use.
PM: How do you envision the role of autonomous vehicles like the IAV evolving in the next 5-10 years in the industrial sector?
EG: I am confident that vehicles like the IAV will establish themselves as the new norm. Similar to how robotics revolutionized industries over two decades ago, automated vehicles are poised to become the standard for transporting products within facilities. I firmly believe that seamless integration will be pivotal for the success of such projects. With ProMach offering a comprehensive solution from inception to completion, it sets the foundation for success for any company aiming to embrace automation.
For a glimpse into the original IAV customer’s experience, watch the video linked below (the design of the IAV has evolved significantly since then) and download the white paper here.
Click here to interact with the IAV in a special 3D animation on the Quest site
* https://www.futuremarketinsights.com/reports/autonomous-vehicles-market#:~:text=The%20global%20demand%20for%20autonomous,registering%20a%20CAGR%20of%205.6%25.