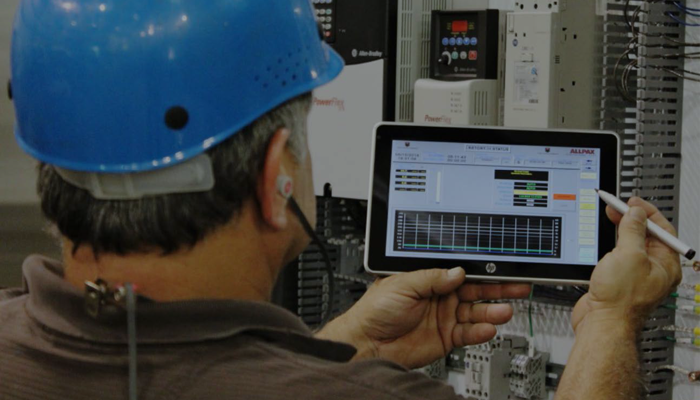
When it comes to food safety and quality, the efficiency and reliability of sterilization equipment are of utmost importance. In a recent press release shared by Allpax, a ProMach product brand, and leader in the design and fabrication of sterilization equipment, discusses the modernization of control systems in batch retorts, which is not merely an upgrade but a necessity for maintaining the integrity and efficiency of sterilization processes.
Retorts are crucial in sterilizing packaged foods, ensuring that products meet stringent safety standards. However, like all technology, retort control systems are subject to aging and obsolescence. Allpax’s timely involvement in identifying the seven warning signs of control system obsolescence indicates proactive action against potential downtime, inefficiencies, and quality compromises in the sterilization process.
The seven warning signs highlighted by Allpax are:
- Replacement parts only available on the used market
- Erratic temperature and pressure control conditions during processing
- Waste becoming unsustainable
- Data access and display challenging for process authority personnel
- Controls difficult to learn and use
- Decreasing the number of maintenance personnel who can troubleshoot and maintain the retort
- Downtime increasing and output falling
These indicators serve as a call for industries relying on retort sterilization to evaluate and upgrade their systems.
David Cohen, Director of Software Engineering at Allpax, underscores the longevity and improved output quality that can be achieved through control system updates, provided the retort’s shell and doors remain sound. This insight opens a window to understanding the intricate balance between maintaining existing assets and embracing new technologies for enhanced performance.
Allpax’s approach to modernization is comprehensive. It begins with an audit of the retort shell integrity and control system. This audit paves the way for a tailored action plan, including recommended upgrades or replacements. The emphasis is on replacing outdated components with easily obtainable, off-the-shelf items, such as PLCs, HMIs, and servers. The possibility of retrofitting existing panels or building new ones further demonstrates the flexibility and commitment to optimizing sterilization processes.
One of Allpax’s recommendations is integrating the company’s basket tracking system in every modernization project. This system ensures each product basket undergoes the correct sterilization process, dramatically lowering the risk of product recall—an important concern in the food and beverage industry. Moreover, adopting new control systems facilitating remote access marks a significant leap towards minimizing downtime, offering real-time technical assistance that can swiftly address any operational hiccups.
Allpax’s commitment to complying with FDA processing guidelines, including 21 CFR Part 11, and the ability to generate batch reports automatically, signals a significant advancement in meeting regulatory requirements and enhancing operational transparency. This transition supports regulatory compliance and contributes to a more sustainable and efficient operation.
Allpax’s insights into retort control system modernization provide a clear roadmap for businesses to enhance their sterilization processes, emphasizing the need for technological adaptation to maintain competitiveness and compliance. This showcases Allpax’s leadership in sterilization technology and highlights the broader implications for the food and beverage industry, reinforcing the critical role of advanced solutions in safeguarding food quality and safety.
Read the full press release below to learn more about the seven warning signs Allpax identifies. Click here to visit the Allpax page and contact a retort specialist. And click here to visit their retort reconditioning, rebuild, and upgrade services page.